Maintenance Program Options & Implementing A Predictive Program
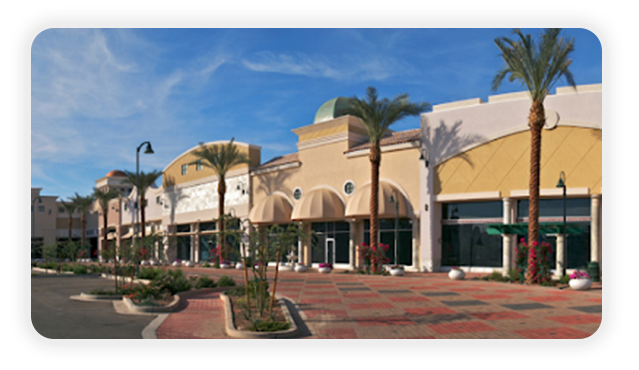
Preventive maintenance programs keep equipment running smoothly through preplanned cleaning, lubrication, adjustments, repairs, and component or system replacements. Facility and energy managers use preventive maintenance routines to monitor and reduce any wear that occurs through normal daily operations, prevent costly downtime, and reduce maintenance costs. Every preventive maintenance program relies on a methodical, scheduled approach to support functionality, safety, and sustainability while keeping costs within budget.
Implementing a solid preventive maintenance program requires attention to detail. Facility and energy managers are responsible for keeping detailed records, scheduling, assigning work orders, and maintaining oversight. Logging the type, age, and maintenance data for all assets covered by a preventive maintenance program establishes the foundation for the program. Scheduling maintenance routines responds to both equipment and staffing requirements. Oversight involves gathering and analyzing feedback from maintenance teams and checking to ensure that their work covers all the program requirements.
Types of Preventative Maintenance Programs
Total Productive Maintenance
Total Productive Maintenance (TPM) emphasizes maintaining and improving critical assets and operational processes. Depending on the need, the maintenance team may utilize one or a mix of three types of preventive maintenance programs that fit within TPM. Those are:
- Periodic Maintenance
- Predictive Maintenance
- Prescriptive Maintenance
Connecting to IoT and Industry 4.0
Each of the preventive maintenance programs has the same set of objectives based on the eight pillars of TPM that cover every facet of manufacturing and service. In turn, the foundational approach to service illustrated by the TPM pillars also connects to an Industry 4.0 approach for integrating the IoT into daily functions.
The Internet of Things (IoT) has transformed maintenance for facilities. The IoT connects any device containing on/off switching to the Internet and other connected devices. Within facility and energy management, sensors connect devices, equipment, and systems to the IoT-connected devices that can collect and share usage patterns and observe data from external sources. Within facility and energy management, the alignment between TPM and the IoT facilitates the analysis of the data to find the best time to repair or replace HVAC, lighting, and refrigeration systems.
This foundational Industry 4.0 approach leads to achieving well-maintained systems and lower energy costs. Regular maintenance keeps repair costs to a minimum and allows facilities and their customers to avoid serious problems that lead to extended downtime. Because quality maintenance extends the operating life of equipment, maintenance programs also serve as part of the investment in equipment and systems.
Building Management Systems/Energy Management Systems
While a Building Management System (BMS) or Energy Management System (EMS) serves as an intelligent system that monitors and manages core equipment and components, connecting the system to the IoT adds capability. The BMS or EMS can serve as an IoT platform that shows useful information derived from the connected devices, equipment, or systems. The flexibility of a BMS or an EMS matches with the analysis given by predictive maintenance.
Static Data, Updated Data, and Real-time Data
TPM combined with the IoT utilizes static data, updated data, and real-time data. While static data covers manufacturer, model number, configuration, and capacity, updated data includes:
- Equipment age
- Equipment start time
- Number of users
- Load
- Type of processor used
Another set of updated data lists the breakdown history for equipment, replaced components, the data of replacement, and any additional service history information.
Real-time data comes from sensors physically attached to critical equipment and IoT-connected devices that monitor instruments and systems. The sensors and devices capture changes in voltage, pressure, temperature, vibration, load, noise, and lubricant levels.
From there, aggregated data flows over secure communication systems to a central data warehouse for storage, processing, and analysis. IoT software monitors normal and abnormal patterns, detects possible problems, and offers recommendations.
Data Analysis
The analytics tools include algorithms and artificial intelligence to forecast possible outcomes. Data analysis software uses accumulated data about machine performance gained from daily operations and from manufacturers to create a model of normal operating behavior. Facility and energy managers can work with maintenance supervisors to monitor software dashboards to show load patterns, indicate the probability of an asset failure, and analyze the root causes of problems with control systems, HVAC systems, lighting systems, and refrigeration systems.
Predictive algorithms compare real-time data with the model and look for unexpected changes. For example, a slight voltage variation may disclose a potential problem with a compressor in a specific refrigeration system. Machine learning tools within the data analysis software provide the decision analysis needed to identify the best time for a repair or replacement.
While the system operates, predictive analysis enables maintenance, repair, and replace decisions. Decision tools based on regression analysis find patterns in large data sets and pinpoint factors that influence the operation of a lighting system. If the software detects changes from the predicted normal operation, it issues an early warning about possible failures. Sensors may indicate that the heat rate and output power have surpassed an operating threshold.
Planned Maintenance Follows a Schedule
Also referred to as time-based or periodic maintenance, planned preventive maintenance occurs at scheduled intervals during a calendar year. Equipment manufacturers often provide Mean Time Between Failure (MTBF) averages and recommendations for periodic maintenance. This information helps determine the best maintenance intervals for equipment. Each regular maintenance routine also provides data to be used to adjust weekly, monthly, quarterly, or annual schedules.
Typical planned preventive maintenance programs include:
- Inspecting the system for any signs of corrosion.
- Checking that moving parts have the proper lubrication
- Replacing filters
Along with those checks, most programs also verify that pressures and temperatures remain within recommended ranges. As the below chart shows, a facility maintenance team applying a periodic maintenance program to HVAC systems may address different types of potential problems with annual or seasonal and monthly schedules.
Prescriptive Maintenance Offers Solutions
Prescriptive maintenance (RxM) utilizes the same sensor/device/IoT connectivity seen with predictive maintenance but adds another layer of uptime maintenance. The difference between the two maintenance technologies exists through the software that powers RxM.
While both predictive and prescriptive use machine learning, the prescriptive analysis software is built around machine learning tools that not only analyze the condition of equipment but also assess the level of operational risk associated with the condition. While predictive maintenance may trace back to a manufacturer’s MTBF data and predict the best cost-effective schedule for maintenance, prescriptive maintenance pushes individualized recommendations to a maintenance supervisor.
Predictive maintenance utilizes historical data to show trends and establish benchmarks. The analysis of those trends leads to estimates about the possibility of failure. Prescriptive maintenance takes the analysis several steps further by tracking variable conditions, including units' runtime and airflow across coils and filters. In brief, the software identifies options that could cause an equipment failure and then shows the most likely scenario.
Prescriptive Maintenance Helps Prioritizing Maintenance
Analytics software facilitates closed-loop control for balancing the demands of facility management. Aggregating measurements such as Delta T with other data sources provide a clear picture of system operation and capabilities. There are also models to adjust for the impact of changing weather conditions on customer comfort to prioritize the best resources. Given the data analysis, maintenance supervisors/teams can prioritize maintenance--or even postpone maintenance on assets that have a lower priority.
For facility and energy managers, prescriptive maintenance offers the potential for increasing service-level productivity. RxM allows a technician or a small team to cover multiple facilities spread over a wide region. In some instances, the software may recommend a repair or replace option. In others, the analytics may recommend that facility managers change the operational characteristics of equipment so that the equipment operates until a scheduled downtime.
Prescriptive Maintenance Large-scale Benefits
Facility and energy managers experience tangible benefits when applying predictive maintenance (PrM). The capabilities found within Predictive Maintenance occur through artificial intelligence and machine learning. Artificial intelligence (AI) allows computing systems to mimic human behavior and decision-making. Computer technologies combine algorithms with massive datasets to enable problem-solving. Each artificial intelligence algorithm can make predictions or provide classifications by analyzing input data. Predictive maintenance prioritizes the data and utilizes AI algorithm-based recommendation engines to discover trends and make service recommendations.
Reduce Downtime with Predictive Analysis
The use of data analysis to proactively identify potential problems allows facility and energy managers to prioritize maintenance tasks and avoid unplanned downtime. The advantages of predictive maintenance include:
- Fewer breakdowns
- Reduced downtime
- Decreased costs
- Improved safety and comfort
Aside from the technical aspects of PrM, a predictive maintenance system's success depends on interaction with and between people. With analytics software pinpointing the location of the probable fault, technicians can make better decisions about the parts needed for a repair.
In addition to informing better decisions about resource management, predictive analytics can lead to faster responses to critical maintenance issues. Regular preventive maintenance routines may miss subtle signs of underperforming older equipment that can lead to a breakdown. However, predictive analytics can prevent downtime by identifying problems and conditions that cause equipment or component failure.
Reduced Costs
Predictive maintenance's advantages provide the ability to align maintenance strategies with corporate ones and cultivate customer relationships through safe, comfortable working environments. Fewer breakdowns translate into less stress for maintenance teams and improved energy efficiency. Strategic alignment exists through insights that disclose the level of impact on operations and the effective use of resources. With all units within a corporation competing for annual allocations, predictive maintenance offers a cost-saving advantage.
For example, predictive maintenance uses HVAC systems begins with multiple data streams flowing from sensors attached to compressors, chillers, motors, refrigerants, and water supplies. These ongoing data streams accumulate in real-time, compare with historical and usage data, and combine with weather data to produce terabytes of information. Predictive maintenance sorts through the data and uses analytics to discover potential problems and determine the best maintenance schedule.
Using AI to Know When to Repair vs. Replace
Machine learning works within artificial intelligence and uses algorithms and data to imitate how humans learn. Statistical analysis within the algorithms allows computing technologies to uncover insights about large sets of data. Once the computer system finds an actionable insight, it drives decisions within applications.
- Fewer breakdowns
- Reduced downtime
- Decreased costs
- Improved safety and comfort
Predictive maintenance monitors equipment condition through sensors and uses alerts--based on artificial intelligence and machine learning--to notify maintenance teams about the potential for a problem. The decision-making capability found within predictive maintenance uses all data sources to determine the best time for servicing equipment.
Automatic Work Order Triggers and Closing the Loop
Software dashboards provide the human interface for AI and machine learning algorithms. Dashboards typically show criticality and risk scores and other information about systems that can inform operational decisions. Graphs, charts, and tables illustrate the current state of equipment or components and generate work orders. Dashboards also show work queues for specific equipment or components and use pre-configured lists that illustrate work-in-progress and show service completion for assets.

Implementing Predictive Maintenance
As with all major initiatives, implementing a predictive maintenance program involves defining requirements, determining corporate and maintenance benefits, and establishing necessary infrastructure. Each of those process steps should align with the eight pillars of Total Productive Maintenance. Defining the requirements for a PrM occurs through an awareness of corporate, staff, and customer needs, the functional aspect of pulling data from sensors into a data repository for analysis, and the transitional aspects of moving from the routines of condition- or periodic maintenance.
Identifying the Equipment that Will Connect to PrM
The scope of a PrM program has a direct impact on all requirements. Decisions about the type of equipment, devices, and systems connected to the IoT through sensors impact the type of data analyzed by PrM software and the data sources. Cost limitations may prompt managers to narrow a PrM program and designate which equipment is most critical. Yet, the designation of “critical” may depend on corporate priorities and emphasize customer safety and comfort.
When considering a PrM program scope, it is important to list equipment out by location, indicating the type of equipment, model numbers, serial numbers, and age of equipment. Next, study the maintenance history to determine historical repair and replacement needs.
Identify and Collect Data Sources
Facilities offer diverse sets of real-time data from devices, sensors, and applications that a predictive maintenance system must collect. Defining data sources for one facility or multiple facilities requires Building or Energy Management Systems (EMS), building structural components, and a Computerized Maintenance Management System (CMMS).
Management systems provide numerical data such as temperature, energy consumption, flow rates, and categorical data that includes alarms and operating status. Devices connected to air handling units and chillers monitor vibration, temperature, and lubricants while detecting leaks or breaks in electrical insulation.
Structural data from a facility includes the type of windows and window coverings used in the facility and other factors such as type of construction. The AI analytics used for predictive maintenance learn about and adapt to changes in structural conditions when controlling lighting and HVAC systems. And a CMMS provides data about work orders, user requests, historical data, inventory data, and ongoing maintenance activities.
Machine Learning Requires Training, Validation, and Testing
Solving the functional aspect of implementing predictive maintenance depends on the data quality used to accurately predict the correct schedule for repairing or replacing equipment. Training, validation, and test data establish the predictive modeling algorithms need to learn from existing data. Machine learning uses training data to build its algorithmic muscle. A training data model constantly evaluates data, discerns behavior trends from the data, and then adjusts to match the purpose of predictive maintenance with HVAC, lighting, and refrigeration systems.
An effective predictive maintenance program revolves around adjusting to new conditions and unseen or unexpected data. Validation data pushes training data to new levels by introducing unseen data into the machine language training model. The use of non-evaluated data tests the capability of the machine learning tools to make accurate predictions based on new data without having a defined relationship between features and targets. Machine learning models receive repeated testing to ensure the accuracy of all projections. Test data completes the circle of training, validation, and testing for machine learning algorithms by repeatedly using unseen, non-evaluated data to check the capabilities of algorithms.
PrM Integration Impacts on IT Teams and Vendors
There are a lot of impacts a PrM program can have on IT teams. A PrM program impacts IT support because of the requirements for new software tools and cyber-secure connectivity. A PrM also introduces a series of changes for technicians accustomed to periodic maintenance routines. The resulting emphasis on technical training may require external support or work by an internal training group.
While technicians and IT support staff may require additional resources and training, facility and energy managers must ensure the quality of data and system-wide accountability for making data-centric decisions. Implementing a predictive maintenance program may also require integration with vendors who provide work order management software. Typically based within a CMMS, work order management software combines with predictive technologies to automatically create a work order when a PrM detects that an asset has fallen out of defined operating parameters. The software also alerts maintenance teams about operational issues.
Predictive Maintenance Saves Money
PrM Integration Impacts on IT Teams and Vendors
Predictive maintenance lowers indirect and direct operating and maintenance costs. As sensors monitor such things as energy consumption and climate information for clusters of facilities, data-driven analytics adapt to customer needs by changing temperature and humidity levels. In addition, the analytics can also apply data obtained from utilities to forecast electricity loads and then determine how to operate the systems while reducing peak demand, decreasing the load of the system, saving energy, and cutting operating costs. An incredible amount of efficiency and cost savings is introduced with predictive maintenance.
Studies show that companies switching from planned maintenance to predictive maintenance realize an average 8-12% annual cost savings. Compared to traditional maintenance programs with an ROI of four to five years, predictive maintenance also offers an ROI of 10 months to two years.
The savings experienced by implementing a predictive maintenance program occur through a decrease in unexpected failures and a decreased need for spare parts inventories. Since the MTBF increases, equipment uptime also increases. Because maintenance teams gain efficiency by spending less time on diagnostics, the amount of time needed for repair also decreases. Software dashboards allow maintenance teams to monitor equipment status without taking the equipment out of service. All of these factors result in reduced maintenance costs.